The advent of 3D printing has significantly transformed various industries, and the medical sector is no exception. One of the most notable advancements is in medical device casting. This article aims to provide a comprehensive understanding of how 3D printing is revolutionizing medical device casting, offering insights for industry professionals.
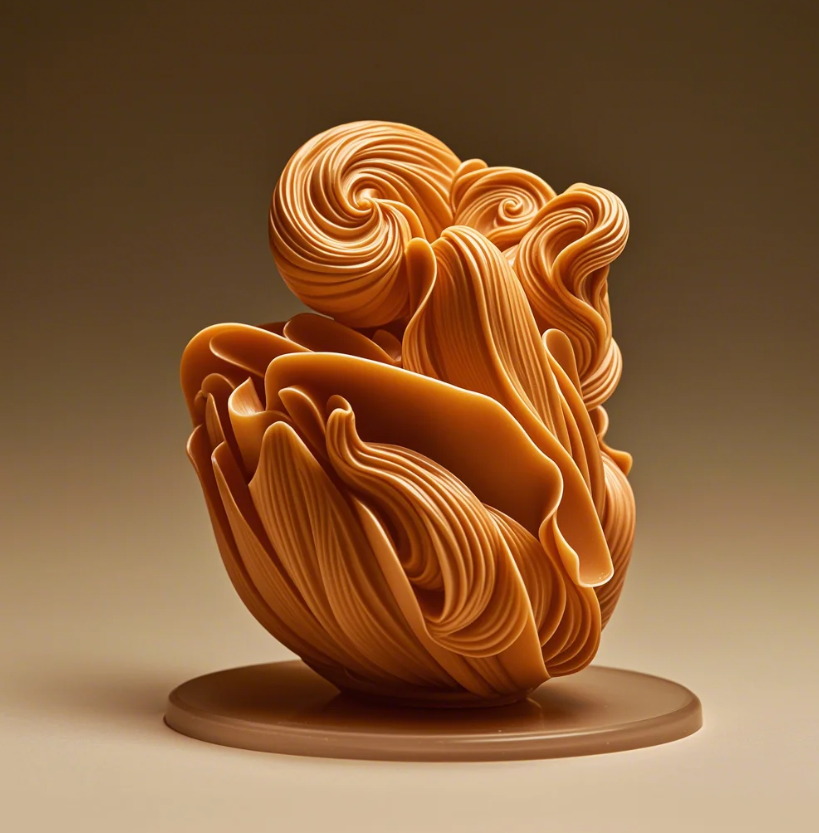
Understanding Medical Device Casting
Medical device casting involves creating precise and customized medical devices using molds. Traditionally, this process has been labor-intensive and time-consuming. However, with the integration of 3D printing, the landscape of medical device casting has changed dramatically. But how exactly does 3D printing enhance this process?
The Role of 3D Printing in Medical Device Casting
3D printing, also known as additive manufacturing, allows for the creation of complex geometries that were previously impossible with traditional casting methods. This technology enables the production of highly customized medical devices tailored to individual patient needs. For instance, prosthetics, implants, and surgical instruments can now be produced with unprecedented precision and speed.
"3D printing has enabled us to create medical devices that are not only more accurate but also more affordable and accessible." - Dr. Jane Smith, Medical Device Engineer
Benefits of 3D Printing in Medical Device Casting
The benefits of integrating 3D printing into medical device casting are numerous:
- Customization: Devices can be tailored to the specific anatomy of patients, improving fit and functionality.
- Speed: Rapid prototyping and production reduce the time from design to implementation.
- Cost-Effectiveness: Reduces waste and lowers production costs compared to traditional methods.
- Complexity: Allows for the creation of intricate designs that are not feasible with conventional casting.
Applications of 3D Printing in Medical Device Casting
Several applications highlight the impact of 3D printing in medical device casting:
- Prosthetics: Custom prosthetic limbs that offer better comfort and functionality.
- Orthopedic Implants: Personalized implants that match the patient's bone structure.
- Surgical Instruments: Tools designed for specific surgical procedures, enhancing precision.
Case Study: 3D Printed Prosthetics
One remarkable example is the use of 3D printing in creating prosthetics. Traditional prosthetics can be expensive and may not fit perfectly. However, with 3D printing, prosthetics can be customized to the exact measurements of the patient, ensuring a better fit and improved comfort. This not only enhances the patient's quality of life but also reduces the overall cost of production.

Future Prospects of 3D Printing in Medical Device Casting
The future of 3D printing in medical device casting looks promising. As technology advances, we can expect even more innovative applications and improvements in the quality and efficiency of medical devices. The potential for growth in this field is immense, and industry professionals must stay abreast of these developments to leverage the full benefits of 3D printing.
For a deeper understanding of the impact of 3D printing on medical device casting, watch the following video:
Conclusion
In conclusion, 3D printing is revolutionizing medical device casting, offering numerous benefits such as customization, speed, cost-effectiveness, and the ability to create complex designs. As the technology continues to evolve, it will undoubtedly play an increasingly vital role in the medical field, improving patient outcomes and transforming healthcare delivery.
Stay informed about the latest advancements in medical device casting and 3D printing to ensure your practice remains at the forefront of innovation.