The textile industry is a vast and intricate field, where precision and attention to detail are paramount. One often overlooked yet crucial aspect is the proper alignment of needles. This seemingly minor detail can significantly impact the quality, efficiency, and overall success of textile production. In this blog post, we will delve into The Importance of Properly Lining Needles in the Textile Industry, exploring its various facets and implications.
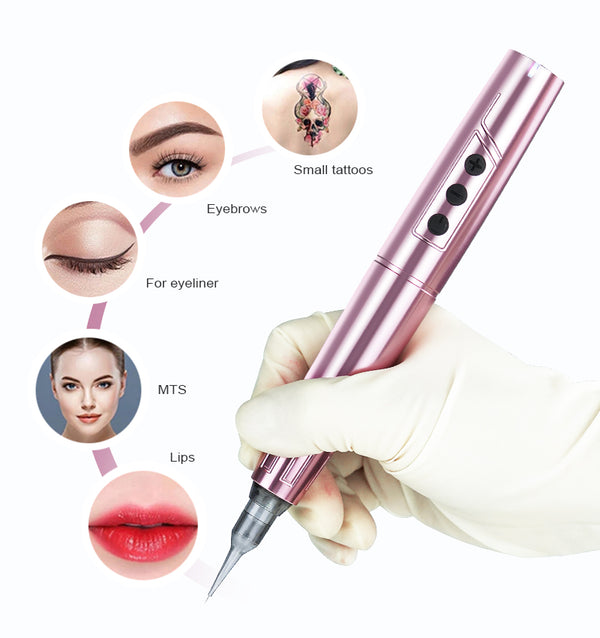
Ensuring Quality and Consistency
Properly lining needles is essential for maintaining the quality and consistency of textile products. When needles are misaligned, they can cause uneven stitching, skipped stitches, or even damage to the fabric. This can lead to a subpar final product, which can tarnish a brand's reputation and result in customer dissatisfaction. By ensuring that needles are correctly aligned, manufacturers can produce high-quality textiles that meet industry standards and customer expectations.
Enhancing Production Efficiency
Efficiency is a key factor in the textile industry, where time is money. Misaligned needles can lead to frequent machine stoppages, increased maintenance, and higher rates of defective products. This not only slows down production but also increases operational costs. Proper needle alignment minimizes these issues, allowing for smoother and faster production processes. This, in turn, boosts overall productivity and profitability.
Reducing Wear and Tear on Machinery
Textile machinery is a significant investment, and its longevity is crucial for maintaining a profitable operation. Misaligned needles can cause undue stress and wear on the machinery, leading to more frequent breakdowns and the need for costly repairs or replacements. By ensuring that needles are properly lined, manufacturers can extend the lifespan of their equipment, reduce maintenance costs, and avoid unexpected downtime.
Improving Worker Safety
Worker safety is a top priority in any industry, and the textile sector is no exception. Misaligned needles can pose a risk to operators, as they may cause needle breakage or other malfunctions that could result in injury. Proper needle alignment helps to create a safer working environment by reducing the likelihood of such incidents. This not only protects workers but also fosters a culture of safety and responsibility within the workplace.
Examples of Proper Needle Alignment in Practice
Consider a scenario where a textile manufacturer is producing high-end garments. The precision required for these products is immense, and even the slightest misalignment of needles can result in noticeable flaws. By implementing strict protocols for needle alignment, the manufacturer ensures that each garment meets the highest standards of quality. This attention to detail not only enhances the final product but also reinforces the brand's commitment to excellence.
Another example can be found in the production of industrial textiles, such as those used in automotive or aerospace applications. These textiles must adhere to stringent specifications and performance criteria. Proper needle alignment is critical in achieving the necessary durability and reliability. By prioritizing needle alignment, manufacturers can produce textiles that meet the rigorous demands of these industries.
Conclusion
In conclusion, The Importance of Properly lining needles in the Textile Industry cannot be overstated. From ensuring quality and consistency to enhancing production efficiency, reducing wear and tear on machinery, and improving worker safety, proper needle alignment plays a vital role in the success of textile manufacturing. By paying close attention to this often-overlooked detail, manufacturers can achieve better outcomes, higher customer satisfaction, and a more profitable operation. As the textile industry continues to evolve, the significance of needle alignment will remain a cornerstone of successful production practices.